mirtazapine 45 mg buy online uk
buy mirtazapine
uk
buy abortion pill
buy cheap abortion pill
viagra coupon 2016
pfizer coupons for viagra
progesterone basse
progesterone
effet
mixing adderall and weed
mixing
viagra and weed
tadalafil generico quando
generico cialis 5
mg
gabapentin pregnancy risk
gabapentin pregnancy
study
REVERSE THRUST FOR SEAPLANES
Most casual discussions of hand-propping begin and end with the admonition “Don’t.” That’s not bad advice, except when there’s no other way to start the engine. In fact, hand-propping is a time-honored practice, dating to the beginning of heavier-than-air flight. That it’s still employed says as much about the legacy of aviation as it does our ability to manage risk.
Of course, hand-propping may not be for you. In which case, you need to get either a fully charged battery or a different airplane. If neither are an option, the key to safely hand-propping and airplane engine is proper training and good technique. The best thing about learning the art of hand-propping is that it puts you in touch with some of the finest people in aviation—old timers—and their airplanes.
Getting Started
The best and safest planes to hand-prop are ones that require it by design. Old-school planes like Champs, Cubs, Luscombes and Taylorcraft of a certain vintage fall into this category, as do a number of ultralights and even some modern light sport models. If you want to learn how to hand-prop a plane, this is the category to start with.
Aircraft designed to be hand-propped have specific procedures to follow, a description in the owner’s manual or POH for that particular aircraft. More importantly, for a given make and model, there is a wealth of tribal knowledge and prospective teachers with experience to show you the way. Given the consequences of doing it wrong, natural selection thins the herd of bad teachers pretty quickly.
The difficulty in hand-propping an engine increases with its displacement and compression ratio: It’s easier to hand-prop a smaller four cylinder engine with low compression than a six- or nine-cylinder one with higher compression. Additionally, as the engine gets bigger, the number of people with experience in the procedure quickly drops.
You will find more people comfortable flinging the prop on a Continental C-65 than you will with experience propping an IO-550, Lycoming -540 or a Jacobs radial. Some would argue the bigger behemoths can still be hand-propped in theory, but it gets less and less advisable because it requires more and more umph. “Umph” in this instance is defined as the combination of muscle, weight, leverage and momentum. Not only will you find umph in short supply on larger engines, you will also find a dearth of teachers. Finding a good teacher may not be as easy as finding a CFI, but it is much better than trying to teach yourself.
How It Works
When it comes to lighting the fires, most certified piston aircraft engines remain firmly entrenched in technology’s Paleolithic era. While the automobile industry abandoned the magneto-driven ignition systems back in the days when rock music was still scandalous, most aircraft engines still rely on magnetos. While archaic, there is a reason: Magnetos fire even when the battery and alternator are dead. If you are among the hoi polloi with magnetos, your engine was designed to be started by turning the prop with the magnetos “hot.”
In flight, a typical dual magneto-driven ignition system is set so the spark from both magnetos fires when the piston is 25 or so degrees before top dead center of its stroke. At high rpm, this is what you need to develop optimum power. At high rpm, magnetos are also spinning fast enough to generate lots of electrical potential.
Because the prop is at low rpm during start up, the magnetos can’t provide enough juice to fire the plugs and start the engine. One way of overcoming this problem is installing an impulse coupling on at least one magneto. Another way is the so-called “shower of sparks” technology, which dates from early automobiles and generates the needed extra spark via a device powered by the ship’s battery. Of course, if there is no battery, or it’s dead, you’re not going anywhere.
The impulse coupling, instead, is designed to load spring energy as you rotate the prop. This energy is released at the proper time—late, or “retarded”—to generate spark to light the fires. When you pull a prop through, you may hear the click of the impulse coupling. If the magnetos are off, this will be a click; if they’re are hot, it should be a bang and start.
When the engines reaches a few hundred rpm, the impulse coupling disconnects and timing goes back to the fixed value specified. At this point, your job is simply to stay clear of the spinning blade of death to which you are uncomfortably close.
During engine start, however, the right magneto is usually grounded, making the left magneto the “firing magneto” during start up. This is not universally true, but is the standard configuration for most aircraft engines. During start up, the left magneto uses an impulse coupling with timing retarded to fire on or near top dead center. This allows the engine to catch at low rpm. For hand-propping, it is important to know which magneto has the impulse coupling and use that magneto position for the “hot” position during the start sequence. dual impulse couplings start on both.
The Rules
Before we go any further, we'll outline the three, inviolable rules for hand-propping:
1. Don't get hit by the prop.
2. Don't let the airplane get away.
3. Don't be stupid.
Basic Techniques
There are almost as many techniques for hand-propping as there are types of airplanes. Okay; not really, but there are too many variables to give a cookie-cutter answer other than, “It depends.” But let’s start with some basics. First, whenever you touch a prop, assume the magnetos are hot. A finely tuned engine at the right temperature will fire up on that first click. It will never hurt to verify the mags are in the off position.
Front or Back: When I bought my Cub, I learned to prop it from the front. This became the most comfortable process for me. After refinishing the prop, I repositioned it so it was loaded and ready to pop at the 11 o’clock position when standing in front the aircraft. I did so to facilitate propping from behind the aircraft. Why is this important? Two answers: skis and floats.
Standing in front of a plane that doesn’t have brakes is a clear violation of rule #3, above. Also, it’s much safer to be behind a spinning propeller than in front of it. It took awhile to get used to, but it is now my go-to approach. It may not work for shorter pilots.
Proper Engine Setting: My Cub is set to start with the throttle at idle. If an airplane needs a bit of forward throttle, you are asking for it. If it needs a lot of throttle tampering to get started, you are playing with fire.
The Right Grip: You obviously have to have a good enough grip to impart the energy and momentum into the prop, but every recommendation is to avoid any fingertip wrap around the prop edge. One reason is to avoid the sharp pain that comes when the prop kicks back in the opposite direction. If your fingertips are wrapped around the prop, they will feel the full brunt of this kick back. It stings—a lot. If you overwrap your fingers, you will eventually get “calibrated.”
Another good reason to avoid over gripping the prop is to negate the tendency of using your grip on the object in front of you to assist in your balance. If you have to hold on to the prop to have good balance, you are itching for a violation of rule #1. If you are on an icy/muddy ramp that requires holding onto the prop to maintain your footing, you are already violating rule #3.
Another variable on grip is distance from the prop’s hub. The further out you go, the more leverage; the closer in you go, the more speed you can impart with a single down stroke. The physics for this varies with your body size and strength in relation to the aircraft/propeller size and the umph needed to get it through the compression. Most people find the sweet spot about midway down the propeller blade. For high-compression beasts, you will be heading further out toward the tip.
Good Footing, No Loose Clothing and Smooth Movements: You want to start in a comfortable position with no loose or uneven surfaces. If propping from the front, you also want wheels chocked, someone on the brakes and an exit path without tripping hazards. Though sometimes dashing in appearance, avoid scarves and other loose clothing. The most important thing is your motion needs to be smooth and stable. If the motion feels awkward and imbalanced, it’s likely you’re doing it wrong.
As important as the right footing is, having enough momentum during the swing is perhaps more important. The key is to control the direction of your body’s CG when in and immediately after the snap down on the prop. I have seen old-timers use a leg to help kick their momentum away. This motion starts with one leg lifted and forward. As you pull the prop down, the leg swings back. I have also seen two-handed side throws that attempt to impart side momentum away from the prop.
There are too many body types for me to critique style and it is something kinesthetic that one should witness and feel; it is not the kind of thing you learn from reading about it. After the engine starts, the prop disc is invisible. Don’t walk into it when you see the wheel chocks still need to be removed.
The Right Plane: There are too many NTSB reports that involve electrical failures, gear-up landings and other mayhem that begin with hand-propping an aircraft that should have stayed on the ground. These are not “hand-propping” accidents per se, but the one link in the accident chain involves hand-propping an aircraft successfully in order to briskly fly it to the location of the accident. This is the true reason for rule #3. It is stupid to hand-prop an airplane that a reasonable pilot would deem not airworthy.
As stated earlier, the best plane to hand-prop is one without a starter. Taildraggers are considered easier to hand-prop because the angle you are pulling the prop down also takes your momentum away from the soon to be spinning blade. Planes with three-blade props are eschewed because you have significantly less room between your downstroke and the next hand chopping blade swing when the engine catches. It doesn’t mean it can’t be done, but the further away from the norms you go, the more alone you will find yourself until you become a single outlier or—worse yet—a natural-selection event.
A Safe Partner
While it’s nice to have another pilot helping out, it’s not always practical. Regardless of who helps, he or she must be thoroughly familiar with the controls and must be seated in the airplane with the brakes set.
Like other aviation procedures, the technique involves read backs to assure proper procedure. The AFH provides the standard hand-propping procedure in better detail than my Cub’s POH, which simply says, “Start engine by pulling the propeller through with a snap.”
If the person sitting in the plane doesn’t have the training or competence, you have violated the procedure in the AFH, as well as our rule #3. At this point, you are at risk of getting your pilot certificate revoked, not by the FAA, but by the person you have just put in charge of a 1000-rpm chopping machine you’re standing in front of. Rules #1 and 2 also are at risk of being violated. If you have to explain what magnetos, throttle and mixture control are to the person sitting between you and the death disk, you’re guilty of multiple violations of rule #3.
Solo Propping
It’s hard to find any reference in which solo propping is recommended, yet it is equally hard to find a Cub, Champ or Taylorcraft pilot who hasn’t done it. My Cub’s owner’s handbook says, “Chock wheels OR have occupant who is familiar with controls set brakes in cabin.”
The reason solo propping can’t be ignored comes back to skis and floats. You don’t need someone holding the brakes on an aircraft that doesn’t have them. The biggest risk for solo propping is violation of rule number #2, and turning your plane into a UAV.
When solo propping, you need to have a bomb-proof solution to assure that rules #1 and #2 remain inviolable. There are techniques using glider tow hooks, slip knots, chocks and propping from the rear. You can also turn off the fuel shut valve at the outset. This allows enough gas in the lines to keep an engine running briefly after startup, but not long enough to self-launch your new UAV conversion into the next county. Still, solo hand-propping is best accomplished from behind the prop, perhaps standing on a float.
Starting For Keeps
An electrical system with a starter is a luxury some airplanes don’t offer. Learning to hand-prop is as much a requirement as, say, knowing the airplane’s systems, limitations and airspeeds. For these operators, hand-propping accidents are rare, but do happen. For the rest of us, hand-propping might be an anachronism, a leftover from bygone days when goggles and scarfs were used alongside roadmaps in open cockpits. Until the battery fails at some remote airstrip, at least. Then hand-propping becomes a
The takeaway here is the procedure can be quite risky, of life, limb and sheetmetal. But with some knowledge, some practice and some safeguards, it also can be routine.
Rust Never Sleeps
The big issue is that even the well taken care of 35-year-old plane may look fabulous on the outside with fresh paint and interior, but there will be corrosion in varying degrees, some of it in extremely dangerous places. (At least with planes that have not spent their entire time in a climate-controlled hangar and hardly ever flown.)
Many planes have had both good, attentive owners and far less caring types (hey it’s just a machine. No—it’s a bauxite-based life form). Most owners feel strongly about their airplane.
And just as important was how well the plane was protected from the environment for all those years, as was how often the plane flew and in what kinds of weather, and how it was cleaned on both the inside and outside, and how frequently.
Some poor planes worked their lives for training schools and had a truly tough time in many respects, though their problems may more be from hard use and abuse, while others may have been hangar queens. The point is at these ages, corrosion condition is all over the map on the same age planes.
We Need a Voluntary Corrosion Inspection Program
Most of it you can do on your own when you do your annual preparation or other routine work on the plane. I don’t know how different I am from other owners, but I loved being in and around the plane always inspecting. I continue to both see and read about near disasters, and with these older planes still the vast majority, we are often looking at corrosion as the cause or instigator of the failure,
Work with your Engineer, Tell him why you are interested and any should (all have different planes they may be particularly knowledgeable about) will tell you where to look in your particular airplane (or he can give you the name of an Engineer who can tell you) for common trouble spots.
Then you don’t have to wait a year between checks for problems, as that is too long on old planes in my view. What I’d like to see is proactive owner extra efforts to keep an eye out for corrosion. We have to be careful here to stay legal and not start disassembling the plane unless under supervision, say for an owner annual. Though it would be fine to do some dissembling, checking, lubrication and reassembling with trusted approval. Check with your Engineer first. Some want the plane untouched.
Actually some owners and mechanics make a case for too much inspection and disassembly that can end up doing more harm than good, although I never bought into this argument if the inspection is done properly.
The last thing we want to see is more Transport legislation, but its possible if we don’t start doing this on our own, voluntarily, there will start to be accidents attributable to corrosion. And if some celebrity or politician gets killed, suddenly there could be way too much of a spotlight on old planes, and additional inspection requirements for all planes over, say, 25 years old or some other arbitrary number—like a special annual checklist for planes over 25 emphasizing corrosion inspection may take place.

|
There are already ACs out on old planes, and fortunately they are generally proactive and helpful. We don’t want to turn the TC against us by having them have to respond to political pressure. The Airborne Vacuum Pump business (who virtually owned the market) went out almost overnight a number of years ago when a Senator who was a passenger was killed some years back and vacuum failure was questionably implicated as part of the cause in a twin aircraft. The son was flying, so pilot error was out of the question. Something else had to be blamed in this case rather than pilot error
There is a bit of a paradigm shift here in that half-decent video scopes are now available at low prices that allow for not having to disassemble planes beyond normal requirements. You just have to make the effort to use them, and not cause damage with careless use, which is possible.
In one recent inspection Corrosion was found on the forward and aft wing spars under the fuel tank spacer blocks (P/N 0523524) in the fuel tank mounting bay. This problem was discovered when the fuel tanks were removed for repair. No visual corrosion indications were noted around the spacers when mounted.” You really need to be on the lookout.
If we don’t start making some special efforts at closely inspecting for corrosion and other vestiges of old age, these old planes are going to start falling out of the sky. Don’t count on a typical annual where the owner wants the cheapest thing possible as a safety guarantee. These are people who actually risk other’s lives, and often try to sneak defects past the Engineer.
Another important way to check is look at the logs to see if important checklist items have been done. All maintenance manuals have these hourly checklists. If not much is recorded in the logs, it’s a bad sign.
Many Wings Are Bolted On
That’s not designed so much to scare you, but most wings such as on a Bonanza have 4 very special bolts on each side that have small adjustments that hold the wings on. The true one-piece wing is a rarity and the Mooney is one of the few such airplanes.
But it doesn’t even have to be the wing bolts that fail from corrosion to take a plane out of the sky, but those are not always as easy to inspect compared to an aileron bolt, which can also take a plane out of the sky if it fails. (Warning—You do not pull a wing bolt out to see what condition it is in. A special tool is used to put them in and remove them properly, as well as a rigging jig and special high torque.)
The same concern holds for all the paint jobs and whether the ruddervators or conventional tails or any required control surfaces have been properly balanced after repainting to assure there is no flutter. There are all sorts of things that over the years can add up to make the plane much more dangerous than it should be. You want to be checking logs carefully to assure these things have been done.
Rust Never Sleeps
I’m not picking on specific items here, just giving some general ideas of very critical items that often just never really get checked, nor were they designed to last indefinitely as we are currently attempting to do in a rather grand old age experiment often left to its own devices on how long a part will last until failure.
|
Click on the following links to view the information provided.
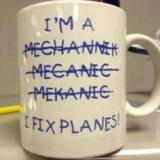